Quality Assurance (QA)
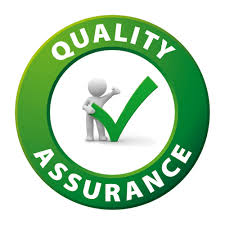
Quality Assurance
Quality assurance (QA) is a way of preventing mistakes and defects in manufactured products and avoiding problems when delivering products or services to customers; which ISO 9000 defines as “part of quality management focused on providing confidence that quality requirements will be fulfilled”. This defect prevention in quality assurance differs subtly from defect detection and rejection in quality control and has been referred to as a shift left since it focuses on quality earlier in the process (i.e., to the left of a linear process diagram reading left to right).
The terms “quality assurance” and “quality control” are often used interchangeably to refer to ways of ensuring the quality of a service or product. For instance, the term “assurance” is often used as follows: Implementation of inspection and structured testing as a measure of quality assurance in a television set software project at Philips Semiconductors is described. The term “control”, however, is used to describe the fifth phase of the define, measure, analyze, improve, control (DMAIC) model. DMAIC is a data-driven quality strategy used to improve processes.
Quality assurance comprises administrative and procedural activities implemented in a quality system so that requirements and goals for a product, service or activity will be fulfilled. It is the systematic measurement, comparison with a standard, monitoring of processes and an associated feedback loop that confers error prevention. This can be contrasted with quality control, which is focused on process output.
Quality assurance includes two principles: “fit for purpose” (the product should be suitable for the intended purpose); and “right first time” (mistakes should be eliminated). QA includes management of the quality of raw materials, assemblies, products and components, services related to production, and management, production and inspection processes. The two principles also manifest before the background of developing (engineering) a novel technical product: The task of engineering is to make it work once, while the task of quality assurance is to make it work all the time.
Historically, defining what suitable product or service quality means has been a more difficult process, determined in many ways, from the subjective user-based approach that contains “the different weights that individuals normally attach to quality characteristics,” to the value-based approach which finds consumers linking quality to price and making overall conclusions of quality based on such a relationship.